En el ‘taller’ de las células CAR-T: fármacos personalizados a escala industrial.
Una pequeña ciudad holandesa esconde el secreto de la fabricación de las células CAR-T, que sigue un ‘patrón’ muy diferente del empleado en la ‘farma’ tradicional. La producción de la terapia celular CAR-T.
La producción de la terapia celular CAR-T
La producción de la terapia con células CAR-T no tiene nada que ver con la fabricación tradicional de fármacos. Como en los vestidos de alta costura, el tratamiento celular se cose a la medida de cada paciente, de forma manual en gran parte del proceso y con un alto grado de precisión y atención al detalle. El reto es que ese tipo de producción tan innovadora mantenga la calidad y seguridad que exige un exponente de la medicina personalizada y que, además, pueda hacerse a escala industrial para llegar a todos los enfermos que lo necesitan.
En la pequeña localidad de Hoofddorp, en Países Bajos, se encuentra uno de los talleres donde profesionales altamente especializados fabrican las células CAR-T de Kite. La compañía, fundada en 2009 en Santa Mónica (California, Estados Unidos) y que desde 2017 forma parte de la biofarmacéutica Gilead Sciences, tiene aquí la tercera de sus plantas dedicadas al desarrollo de la inmunoterapia celular, la primera en suelo europeo.
Con motivo del 5º Congreso Europeo sobre células CAR-T, organizado recientemente por la Asociación Europea de Hematología (EHA) y la Sociedad Europea de Trasplante Hematopoyético y Terapia Celular (EBMT), en Rotterdam, Kite ha abierto las puertas de su planta a un grupo de periodistas de varios medios europeos.
En cuanto se atraviesan las paredes de cristal de este moderno edificio de 19.000 m2 se percibe que nada se ha dejado a la improvisación. No iba a ser menos el emplazamiento de las instalaciones. La planta, que ha contado con una inversión de 135 millones de euros, se encuentra a diez minutos andando del aeropuerto de Ámsterdam Schiphol, en un enclave que conecta por carretera con toda Europa.
No en vano los fármacos vivos que se fabrican aquí deben llegar en un tiempo mínimo a pacientes que ahora pueden estar en Marsella, Florencia, Sevilla o Atenas. Y, lo más importante, durante toda la ruta, desde que los linfocitos T del paciente parten del hospital hacia la fábrica y también durante su viaje al centro donde las espera el paciente, ha de saberse siempre dónde se encuentran.
Harry Smith, director asociado de Global Medical Affairs de Kite, enumera las enfermedades en las que se emplean las dos células CAR-T que se fabrican aquí, axicabtagén ciloleucel (Yescarta) y brexucabtagén autoleucel (Tecartus). Kite, de hecho, ha sido la primera compañía que ha logrado tener dos CAR-T aprobadas por la agencia del medicamento FDA. “Los dos productos se indican en linfoma B difuso de célula grande (LBDCG), linfoma del manto y folicular, y en leucemia linfocítica aguda”. Explica que todas ellas son enfermedades hematológicas malignas que afectan a los linfocitos B, en cuya superficie se expresa el marcador CD19 y diana de estas células CAR-T.
Se producen 4.000 dosis anuales de las
más de 12.800 que fabrica Kite en sus tres centros.
Un tratamiento necesario
En el LBDCG, recuerda que el 80% de los pacientes candidatos a trasplante no alcanzan remisión completa a largo plazo, por lo que las terapias con células CAR-T constituyen una opción totalmente necesaria en esos enfermos. Las cinco indicaciones tienen ya la aprobación de las agencias reguladoras estadounidense y europea.
El ritmo es constante en esta planta donde se producen 4.000 dosis anuales de las más de 12.800 que fabrica Kite en sus tres centros. El personal asume la recepción de la sangre del paciente; comprueba y registra que el material celular cumple con las especificaciones necesarias; efectúa la modificación genética al transducir mediante un vector retroviral el receptor de antígeno quimérico (CAR, en sus siglas en ingles). Así se consigue que unas simples células inmunitarias se conviertan en una potente arma dirigida hacia el cáncer sanguíneo.
Después, ese grupito de células modificadas se expande en incubadoras durante unos días gracias al efecto de ciertas proteínas y factores de crecimiento. De esta forma, se llega a los millones de células que conformarán una dosis única para cada paciente, con la que se intenta recuperar la capacidad defensiva del organismo ante el cáncer.
Una vez obtenida la dosis de CAR-T, se envasa y ultracongela en nitrógeno líquido para iniciar rápidamente el proceso logístico que devuelve el producto hasta el hospital donde le espera el paciente. Ese viaje de vena a vena de las células, se realiza con la organización de Kite en el plazo de 16 días, en Estados Unidos, y de 19, en Europa, expone Smith.
Recientemente, un estudio presentado en la reunión anual de la Sociedad Americana de Hematología (ASH) desveló que la reducción del tiempo de la aféresis a la infusióntenía un impacto claro en los resultados del tratamiento. “Es una línea de investigación en la que estamos profundizando, y esperamos tener datos más concretos pronto”, asegura.
Por los pasillos, más que limpios, asépticos, del edificio dejamos de ver ropa de calle y maquillaje. En su lugar, los trabajadores llevan batas blancas, o si se mueven por las salas blancas, donde tiene lugar la manipulación de las células, deben desnudarse y ponerse pijamas de quirófano, mascarillas, gorros, calzas y guantes.
En el ala izquierda de la planta, un gran almacén que recuerda mucho a los de Ikea guarda todo el material necesario en el proceso, desde los guantes y equipos de protección individual (EPI) a los recipientes desechables donde se guardan las células en las diferentes fases de tratamiento. Cada envase o cartucho que alberga las células está marcado con los datos del paciente.
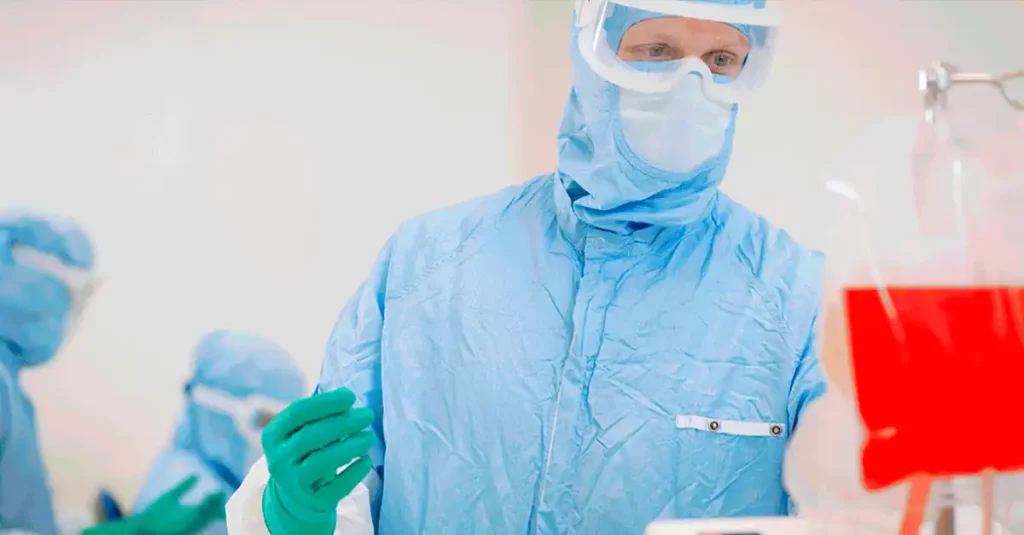
Trazabilidad al milímetro
La terapia se traslada a más de 210 puntos diferentes fuera de Estados Unidos (más de 120 dentro del país), y en todo momento debe estar asegurada la cadena de custodia, sea el transporte por aire o por tierra. Para ello, cuentan con el sistema de seguimientoKite Konnect, un programa que permite saber, tanto al equipo médico que trata al paciente como a la planta donde se desarrolla el fármaco, dónde se encuentran las células. Los recorridos realizados por carretera cuentan con un servicio de mensajería exclusivo; lo habitual es que viajen a la vez dos transportes, así están preparados ante cualquier imprevisto.
Y si la trazabilidad se sigue al milímetro, la descontaminación de potenciales agentes que puedan afectar al proceso también se extreman. El almacén se limpia con frecuencia, y durante la visita nos cruzamos más de una vez con personal de limpieza en plena acción. La zona donde se reciben las células del paciente desde cualquier rincón de Europa recuerda a una sala de mensajería, con las estanterías preparadas para recibir los paquetes; eso sí, está como una patena. Las bolsas de sangre que llegan se desinfectan a mano, en profundidad, en un área específica, antes de llevarlas al área derecha de la planta, una burbuja aséptica que atisbamos a través de cristales.
A lo largo de un pasillo se suceden a ambos lados varias salas blancas, el lugar donde se hace la magia. La planta cuenta con seis salas funcionando, cada una de ellas con varios puestos de trabajo, donde los técnicos manipulan las células de un paciente cada vez.
Pronto se sumarán nuevas salas blancas, cuya construcción se está llevando a cabo en un gran espacio de techos altos, que reúnen lo necesario para asegurar el flujo de ventilación adecuado. Es una condición imprescindible que en estas salas se tenga una atmósfera totalmente limpia y libre de potenciales partículas contaminantes.
Una cuarta parte de las 800 personas de más de 50 nacionalidades que trabajan en la fábrica se dedica expresamente al control de calidad. Su responsable es Marc Kamp. Como director de Quality Engineering and Program Lead GxP Quality Cell Therapy de Kite, se encarga de que a lo largo de toda la cadena de producción y de suministro se cumplan las normas de calidad GxP en la terapia celular (G y P son las siglas de buenas prácticas, mientras que la x atañe a investigación, fabricación o suministro, o cualquiera de los diferentes ámbitos en el proceso de desarrollo y distribución del tratamiento).
400 Páginas por paciente
“Hemos documentado todas las especificaciones del proceso de la A a la Z”, explica Kamp a Diana sobre un procedimiento que han diseñado desde cero. “En la farma tradicional se prepara un informe para un lote que puede abarcar, por ejemplo, dos millones de pastillas.
Con las células CAR-T elaboramos un informe para el oncólogo de cada paciente al que va dirigida la terapia que puede extenderse a lo largo de 400 páginas. Por eso necesitamos a tantas personas en el departamento de calidad, porque hay que comprobarlo todo dos veces, y después, volver a comprobarlo”, enfatiza. “No puede haber margen de error: cualquier mínima confusión puede ser letal”, comenta sobre este engranaje que no para de moverse, por riguroso orden de entrada en la fábrica: “Lote que nos llega de un paciente, lote que se prepara.
Todos los Pacientes son
tratados por igual.
Todos son tratados por igual, porque sabemos que todos los pacientes se encuentran muy enfermos; no es nuestra misión determinar quién va primero. Ni tampoco querría estar en esa tesitura”.
De la eficacia del departamento hablan los números: el 96% de las terapias se fabrican con éxito, “una cifra que hemos mantenido constante desde el inicio”, afirma Kamp, quien recuerda, además, que ese inicio se desarrolló en plena pandemia de covid. “Fue un gran reto desde muchos puntos de vista. Entonces ya estábamos activos y teníamos en marcha la cadena de suministro con las plantas de Estados Unidos, que se vio obstaculizada por la pandemia, pero conseguimos mantenerla con el esfuerzo y la implicación de todo el equipo”, enfatiza con orgullo.
“Al mismo tiempo, estábamos construyendo estas instalaciones y queríamos que estuvieran abiertas para nuestros pacientes sin retrasar los plazos”. Echando un poco de imaginación a esas ganas -poniendo en práctica inspecciones virtuales, colocando cámaras estratégicas, “como si estuviéramos planificando un rodaje”, relata- consiguieron los permisos de las autoridades holandesas a tiempo y, finalmente, “nos las arreglamos para tener la fábrica activa a tiempo”. Desde entonces, asegura, “no hemos parado”.
Los controles de calidad se despliegan a lo largo de la cadena de custodia. Cuando se reciben las células frescas del enfermo, se comprueba que reúnen los requisitos como materia prima. Hay que asegurarse de que todo el proceso está libre de contaminantescomo virus o bacterias, y de que las células CAR-T obtenidas se dirigen con la potencia y la precisión deseadas contra el cáncer. También es importante que no queden células residuales en el producto final. El paso más delicado es, en opinión de Kamp, la transducción del CAR. “Hemos diseñado un proceso robusto, pero quizá esa parte sea la más delicada, pues depende de la naturaleza de las células del paciente”.
La transducción es la parte donde técnicos cualificados y bien entrenados enhebran el CAR en la célula. Es un proceso manual que exige gran precisión y garantías de seguridad. En una amplia sala, una veintena de técnicos recibe formación en las diferentes fases del proceso, desde la purificación o el conteo de las células a la expansión.
El trabajo en la sala blanca es físicamente muy demandante: los movimientos no pueden ser bruscos, hay que mantener máxima concentración y estar atento a todos los detalles; habitualmente, los técnicos no pasan más de cuatro horas trabajando en uno de esos puestos.
En el entrenamiento que se sigue con simuladores durante tres meses se enseña a trabajar con el equipo de protección y guantes. Suele formarse a jóvenes recién graduados en carreras científicas o a profesionales que vienen de la industria convencional y buscan trabajar en un ámbito de vanguardia, o a quienes les motiva saber que están ayudando a llevar un tratamiento oncológico tan necesario a más enfermos.
“Se sienten cerca del paciente. Pueden ver en qué país está o la edad que tiene. Saber que los pacientes para los que preparan las células son más jóvenes que ellos no les deja indiferentes. El trabajo que hacemos les implica, les hace sentirse más responsables”, destaca Kamp. “Creo que en la compañía todo el mundo es consciente de lo que tiene entre manos. Esto no es un medicamento normal; fabricamos un tratamiento para una persona concreta. El paciente está siempre presente”
Más terapia CAR
Si bien siempre hay cabida para las mejoras, es difícil optimizar un proceso tan cuidado y robusto. Marc Kamp apunta que trabajan para mejorar la tasa de éxito -“nuestro objetivo es llegar al 100%”- y aumentar la productividad, de forma que más pacientes puedan acceder al tratamiento en menor tiempo. Confía en que en cuestión de meses, una vez obtenidas las autorizaciones necesarias, parte del proceso se realice de manera semiautomática, tal como se está desarrollando ahora en la planta más joven de la compañía, en Maryland.
En esa mirada al futuro, Clare Spooner, directora ejecutiva de Global Medical Affairs de Kite, destaca el desarrollo de células CAR-T para otras indicaciones, como el mieloma múltiple, e incluso para tumores sólidos, como el cáncer hepático, y enfermedades no oncológicas. También alude al potencial de las CAR alogénicas a partir de natural killer(CAR-NK), que podrían transformar, de nuevo, una industria en constante innovación.
Fuente
‘Diana’, la revista de las Terapias Avanzadas
Sonia Moreno. Hoofddorp
Jue, 02/03/2023
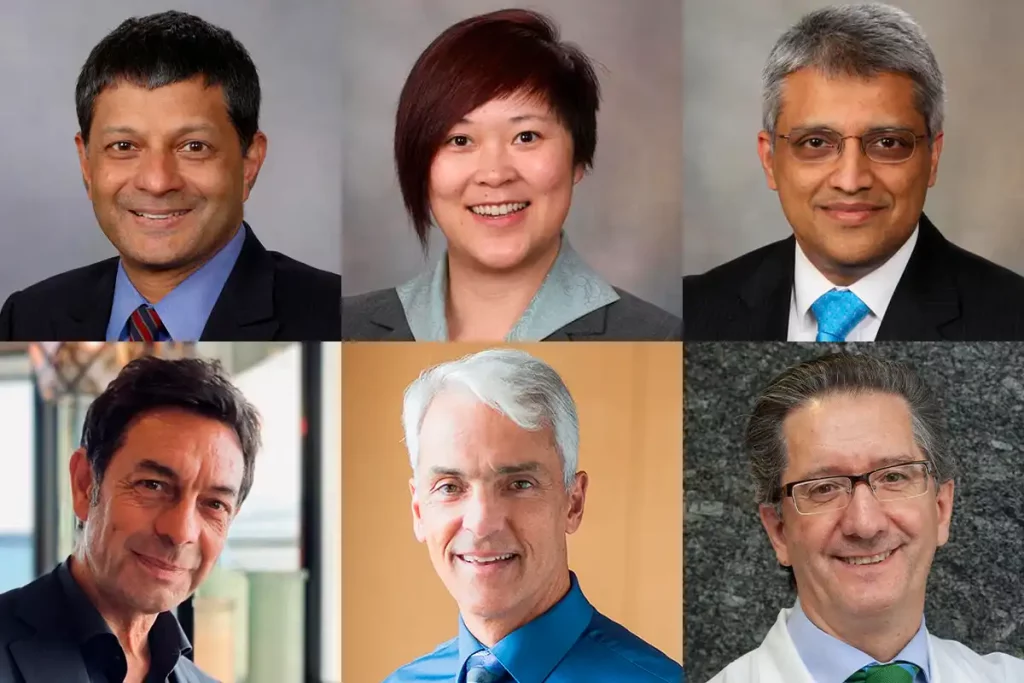
También te puede interesar este artículo.